在制造业、服务业以及各类生产流程中,不良率是衡量质量水平的核心指标,它不仅反映产品或服务的合格程度,更能帮助企业发现问题、优化流程,以下是关于不良率计算的完整指南,结合实际场景,提供可落地的操作方法。
**一、什么是不良率?
不良率指在特定生产周期或服务过程中,不合格产品(或服务)占总量的百分比,某工厂生产1000件商品,质检发现15件存在缺陷,不良率即为1.5%,这一指标直接反映资源浪费程度与质量控制能力。
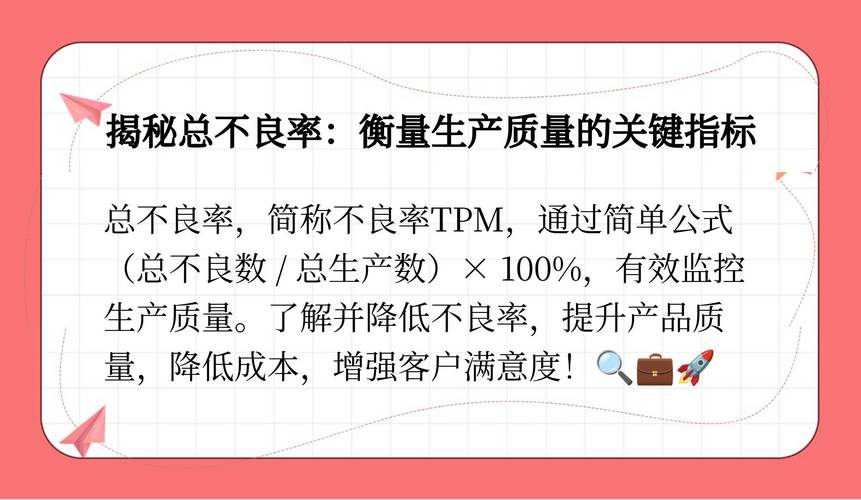
**二、不良率的计算公式
不良率的通用计算公式为:
不良率 =(不良品数量 ÷ 总生产数量)× 100%
需注意两个关键点:
1、数据单位统一:不良品与总生产数的统计周期需一致(如按日、周或批次)。
2、明确判定标准:需提前定义“不良”的准确定义,避免主观判断导致数据偏差。
**三、计算不良率的4个步骤
**1. 数据收集与记录
- 建立标准化质检流程,记录每批次或每日生产总数。
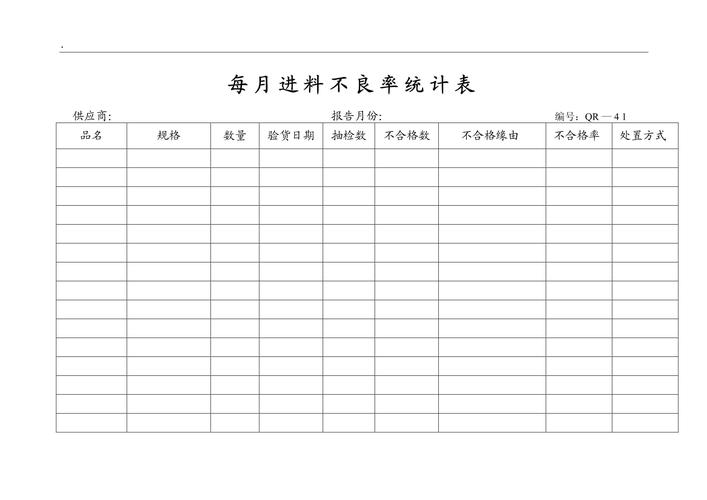
- 使用数字化工具(如ERP系统、电子表格)实时录入不良品数量,避免人工统计遗漏。
案例:某电子厂通过扫码系统自动统计流水线产量,质检员用平板电脑实时标记不良品,数据准确率提升至99%。
**2. 不良品分类
将不良品按类型细分(如尺寸偏差、功能缺陷、外观瑕疵),便于后续分析根本原因。
示例:某服装厂发现80%的不良品源于缝线问题,针对性优化缝纫机参数后,不良率下降40%。
**3. 执行计算
按公式计算结果后,需结合行业标准评估合理性。
- 汽车零部件行业通常要求不良率低于0.1%;
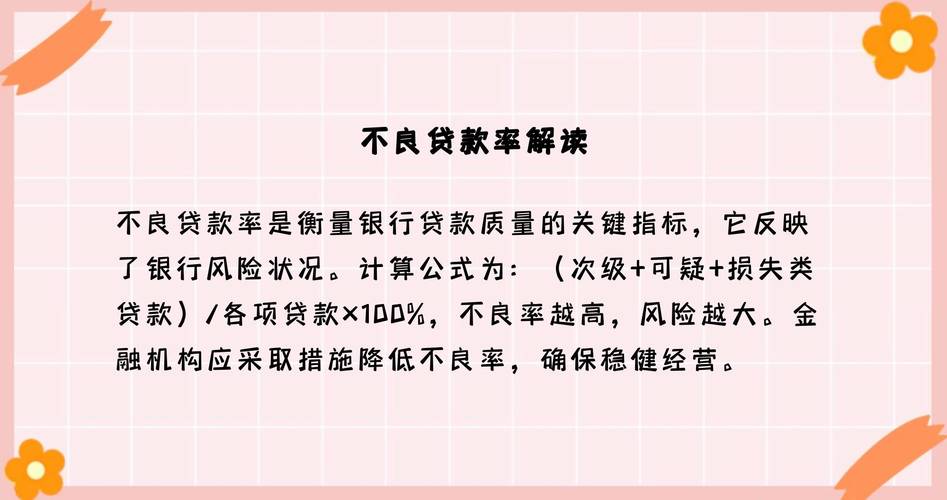
- 餐饮行业菜品出餐不良率可接受范围约为2%~5%。
**4. 结果分析与改进
若不良率超标,需通过鱼骨图分析法或5Why法追溯问题根源,某食品厂发现包装漏气问题源于设备温度波动,调整参数后不良率从3%降至0.8%。
**四、常见误区与解决方案
1、忽略隐性不良品
部分问题可能在后期使用中暴露(如电器元件寿命不足),解决方案:增加长期可靠性测试环节。
2、数据统计口径不一致
如将返修品重复计入不良数,解决方案:明确统计规则,定期审核数据逻辑。
3、过度依赖单一指标
低不良率可能掩盖高成本问题(如过度质检),解决方案:结合“质量成本”指标综合评估。
**五、降低不良率的3个实用策略
1、标准化操作流程(SOP)
为每个生产环节制定详细操作手册,并通过视频培训确保执行一致性,某家具厂通过SOP将工人操作误差减少60%。
2、引入自动化检测技术
使用AI视觉检测设备替代人工目检,可提升精度并减少人为疲劳导致的漏检。
3、建立快速反馈机制
设置产线警报系统,当不良率超过阈值时自动停机排查,避免问题扩大化。
**六、特殊场景下的不良率计算
服务业应用:将“服务失败次数”作为不良品数,快递行业按延误、破损包裹数计算不良率。
小批量生产:采用PPM(百万分之缺陷率)更精准,如生产500件产品中有1件不良,PPM为2000。
质量管理没有“一劳永逸”的公式,但精准计算不良率能为企业提供清晰的改进方向,通过持续监控、分析并优化,不良率不仅是数字,更是推动效率与口碑增长的核心动力,真正的竞争力,往往藏在那些被反复优化的细节里。