仓库盘点是企业管理中不可忽视的关键环节,直接关系到库存数据的准确性、成本控制及运营效率,许多企业因忽视盘点细节导致账实不符,甚至引发供应链中断,本文将系统梳理仓库盘点的实施要点,帮助从业者建立科学规范的操作流程。
一、盘点前的战略性准备
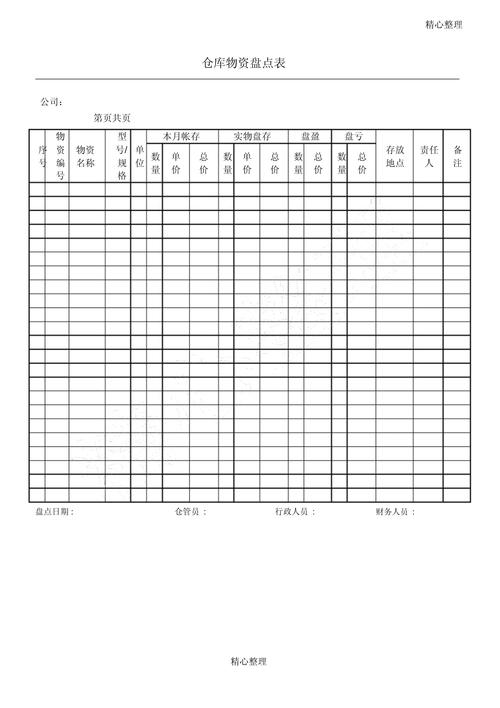
1、人员架构设计
组建由仓储主管、财务人员、操作员组成的跨部门小组,明确分工:主管负责统筹协调,财务人员监督数据核验,操作员执行实物清点,建议引入第三方审计人员参与关键品类盘点,增强结果公信力。
2、环境标准化管理
提前72小时冻结库存移动,设置醒目的"盘点隔离区",对货架实施ABC分类标识:A类高频流转品用红色标签,B类常规品用黄色,C类滞销品用蓝色,整理堆垛时遵循"五距原则"(墙距0.5米、柱距0.3米、灯距0.5米、垛距1米、顶距0.5米),确保消防通道畅通。
3、技术工具部署
配置带红外扫描功能的PDA设备,与WMS系统实时对接,测试网络稳定性时,需模拟200台设备并发操作场景,准备应急方案:当系统故障时,立即启用手工记录模板,要求双人复核签字确认。
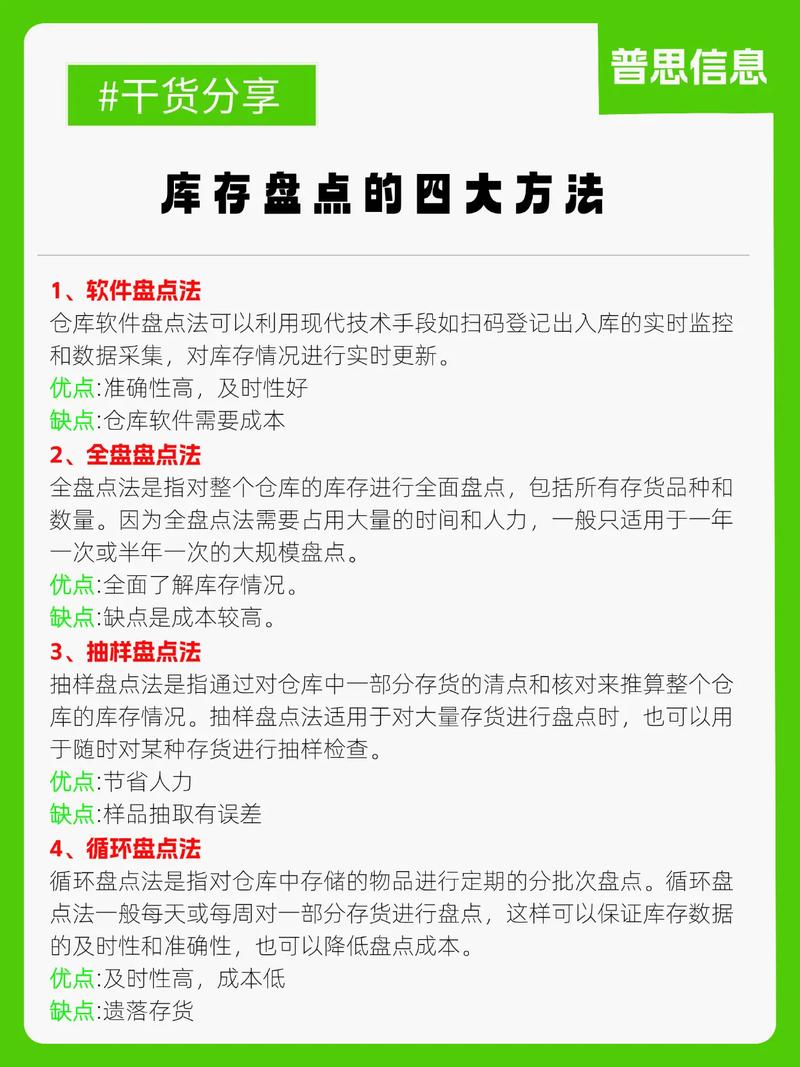
二、动态盘点实施模型
采用"三段式循环法"提升效率:
初盘阶段:操作员按库位分区扫描,系统自动生成差异预警
复盘阶段:不同小组交叉核查初盘数据,重点抽检价值超过5000元的单品
终盘阶段:财务人员随机选取15%的SKU进行盲测,误差率超过0.3%则启动全库二次盘点
对于特殊品类建立差异处理机制:
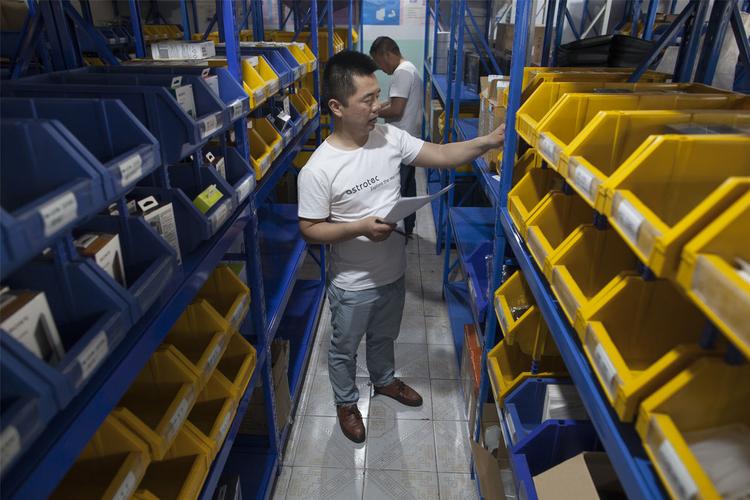
- 易挥发液体采用称重换算,记录环境温湿度
- 精密仪器启用序列号追踪,拍摄实物照片存档
- 散装物料使用定量容器标准化计量
三、数据治理关键点
1、差异分析模型
建立四维分析框架:
- 操作维度:漏盘/重复扫描发生率
- 系统维度:数据同步延迟时长
- 流程维度:单据流转节点耗时
- 物理维度:货物自然损耗系数
2、根因追溯技术
应用5Why分析法深挖问题本质,例如某电子产品盘亏案例:
- 一级原因:系统显示库存100件,实物97件
- 二级追溯:出库记录多登记3件
- 三级核查:扫码枪灵敏度不足导致漏扫
- 解决方案:升级硬件+增加人工复核环节
四、智能化升级路径
引入UWB定位技术,实时追踪货物三维坐标,误差控制在±15cm内,部署AI视觉盘点机器人,通过深度学习算法识别货品状态,准确率可达99.6%,建立数字孪生系统,每4小时自动同步物理仓库与虚拟模型数据。
某汽车配件企业的实践表明:通过部署RFID电子标签,盘点耗时从72小时缩减至8小时,差异率由2.7%降至0.15%,但需注意,技术投入应与业务规模匹配——年流转量低于50万件的仓库,采用条码+平板电脑方案更具性价比。
五、持续改进机制
建立PDCA循环体系:
- 每月召开盘点质量会议,分析TOP5差异项
- 每季度更新SOP手册,纳入最新行业规范
- 每年开展全流程压力测试,模拟极端情况应对
值得注意的是,过度追求"零差异"可能陷入管理误区,合理设定容错阈值:快消品可接受0.5%误差,贵金属则应控制在0.02%以内,重点在于建立差异的快速响应机制,而非单纯追求数字完美。
仓库管理本质是动态平衡的艺术,真正的盘点高手,既能严格执行标准流程,又懂得根据业务特性灵活调整策略,当数据准确性成为企业本能,供应链才能真正成为核心竞争力。